Part 1: WTF are you talking about, Justin?
Well, technically I could just say "add sway bars" to interconnet the suspension, but that's not actually what this is about. Sway bars are U-bars that allow the same motion and resist differing motion. U-bars can perform the effects I'll be talking about, but not when connecting laterally (or longitudinally) adjacent wheels as is typically done. But if you reverse the arm on one end, you turn the U-bar into a Z-bar. A Z-bar allows differing motion and resists similar motion. There are also numerous different mechanisms that can function like a Z-bar that aren't physically a Z shaped torsion bar, but that's a convenient term to use to discuss this idea. So how can you link the corners with Z-bars? Well it has been done numerous times before in the automotive world.
Packard may be the only one to have done this with true Z-bars (torsion) on their "Torsion Level" suspension.

BMC used hydraulics to accomplish the same.
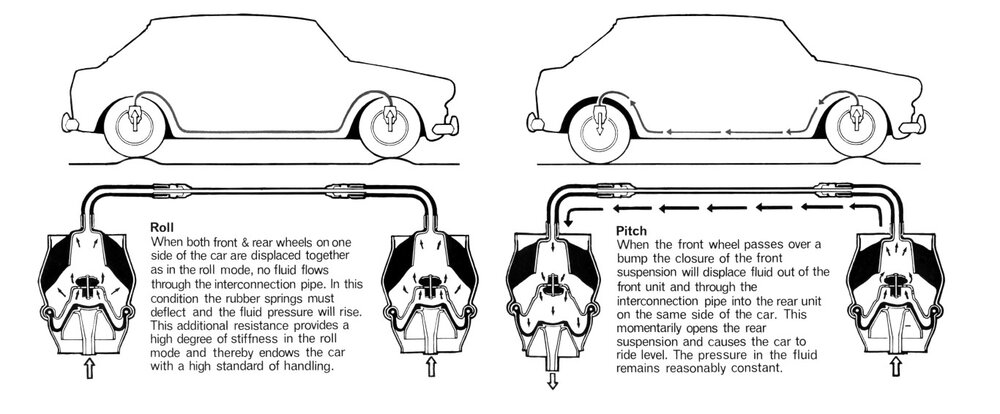
Citroen first did it with coil springs on the 2CV, before doing it hydraulically.

The common theme with all of these cars is that they have been highly regarded for their impeccable ride qualities. This sounds like a 'comfort' thing, and as applied it primarily was. So why am I thinking about it and bringing it up here? Well, because some have also been unusually capable of not sacrificing handling to get that ride quality, and I believe it has further performance benefits that haven't sufficiently been explored as well. The few times these concepts have been applied in professional level racing, they have generally been banned shortly thereafter. But what if at the grassroots level having racecar like performance didn't require a racecar like ride, and still utilized the affordability and simplicity of it still being a fully passive suspension?
With a conventional suspension your 4 corner springs have ride, pitch, and roll all hopelessly intertwined. Changing one mode inherently changes both of the other modes. Adding sway bars only provides the ability to independently add roll stiffness. Additionally, once you're not on a perfectly planar surface (let alone if the surface is less than smooth) your carefully balanced tire loading gets all thrown out of whack. This is why it’s so important for corner balancing to be done on a perfectly level surface. The stiffer you suspension gets, the less tolerant it is of these disturbances.
Now let's take a chassis without any springs and throw some longitudinal Z-bars on it, connecting the f/r wheel pairs on each side of the car a la Packard. The f/r leverage ratios determine the stiffness relative to the CG, which is the baseline most people use for handling balance. The problem is that unless your leverage ratios match your weight distribution, which is not typical considered ‘ideal’ for handling balance, just sitting statically the car will inherently pitch forward or back to the bump stops. And even if it is perfectly static balanced, any load change or dynamic imbalance will have similarly disastrous results. As I understand it, BMC was the only one to not add any additional spring elements. Instead they relied only on significantly progressive leverage ratios that biased the (hydraulic) Z-bars against the imbalance. As a result one of the drawbacks was that they were a bit 'pitchy' despite their otherwise good ride and handling.
You can see in the picture above that Citroen added rubber bellows (springing elements) on either end of the 2CV coil spring canister to ‘control’ pitch. On the other hand, their hydraulic system linked everything and used an engine driven pump to compensate, which goes beyond the scope here.
Packard however added a second pair of springs to the rear axle to carry the imbalance. Here's where it gets interesting through. They added two conventional corner springs to the rear axle. I've seen a sketch of a version with coil springs, but most resources show the torsion bar version (above) that also allowed integrating a load leveling system as well. However, on a car not likely to see large f/r loading variation, like race cars and 2-seat sports cars, these two springs could technically be replace by just a single (3rd) Z-bar. The 3rd Z-bar would basically just be a pitch-only bar that also carries the relatively small imbalance from the leverage ratio vs CG misalignment. In and of itself, and ignoring motion ratio changes with travel, it would have no direct effect on roll and handling balance though, just as the longitudinal Z-bars would no direct effect on pitch.
The 3 Z-bar suspension would result in a fully functioning 4 wheel car suspension, but the 3rd Z-bar would have to be ‘double acting’ where it is reverse stressed at fully droop. By adding a 4th Z-bar opposite the 3rd Z-bar, it they would be able to be ‘single acting’ like the longitudinal side pair can, which means they’d go slack at full droop. The 4 Z-bar system would also be able to variably add ride stiffness, unlike the 3 Z-bar where ride is carried by the side pair Z-bars.
Now I've only been talking ride, pitch, and roll so far, but there is one more motion mode to consider: Twist. You know those one-wheel ramp travel articulation tests that 4x4's like to show off with? Yeah, that's twist.

What does this have to do with pavement performance? Plenty. It goes back to my statement about how performance car suspension setup theory really only holds true on a perfectly planar surface. With a high twist stiffness, as with both independent corner springs and lateral U-bars on high performance cars, as soon as you move one wheel off from planar, the tire loading and handling balance get thrown out of whack. The only conventional way to not do so is how off-roaders do it, which is by lowering your ride, pitch, and roll (spring) rates. But that's bad for performance. Sure any suspension will work if you don’t let it, but what if you could let it work for you rather than against you? By using Z-bars there is as much roll stiffness as you want, but little to no twist stiffness. Non-planar? No problem. Everything from 1-wheel bumps/dips, to cutting across a road crown, to hitting the curbing at the apex, the tire loading variation from all of these plummets. It should be telling that corner balancing also basically becomes a simple function of your f/r leverage ratio, with little regard for how planar the surface is.
Consider hitting a 1-wheel bump while cornering with a conventional suspension. The load on the tire hitting the bump increases, as well as on the tire diagonally across from it. As it lifts that corner of the car, it reduces load on the tires laterally and longitudinally adjacent to it. This is that teeter-totter feeling you get when turning into an inclined driveway, and is what imbalances everything with a conventional suspension… Including the handling balance at that moment.
If you hit that same 1-wheel bump with the (3 or 4) Z-bar suspension, that impact load gets transferred to push down on the laterally/longitudinally adjacent wheel pair and pull up on the one diagonally across. This reduces or eliminates (depending on bump size/speed) the teeter-totter effect, and maintains equivalent tire loading (handling) balance.
Questions, comments, or concerns?... I mean, those other than “It would be cheaper, faster, and/or easier to just do something conventional.”